BASIC COMPOSITION OF WHETSTONE
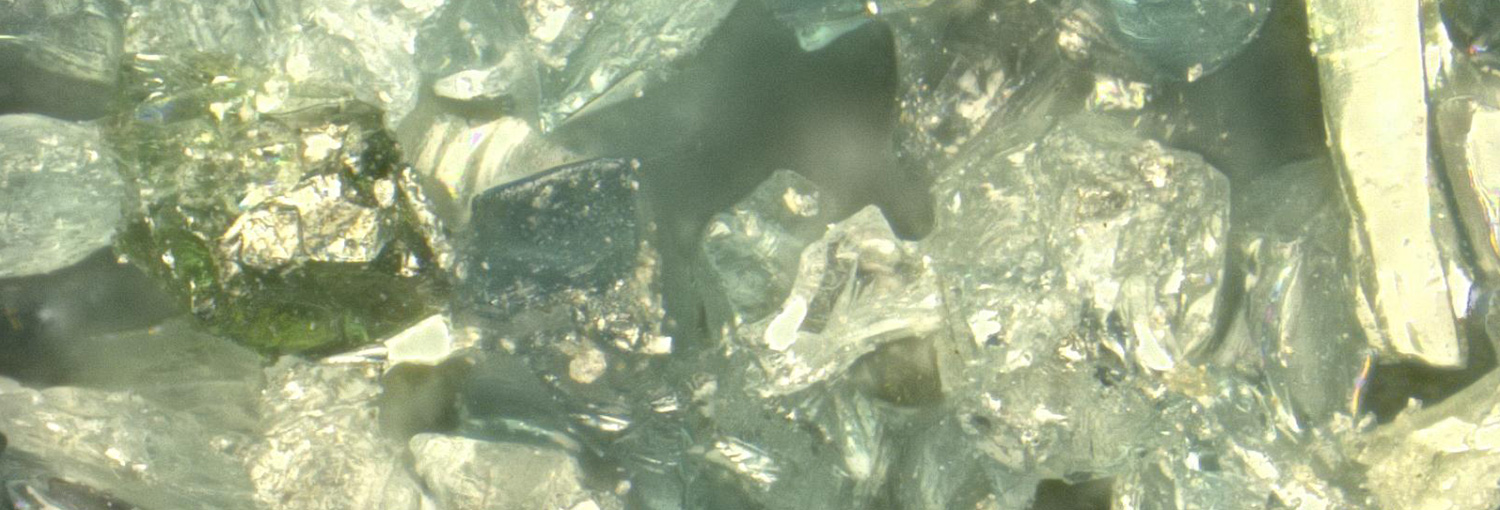
The basics of grinding
Basic composition of whetstone
Three elements, five factors
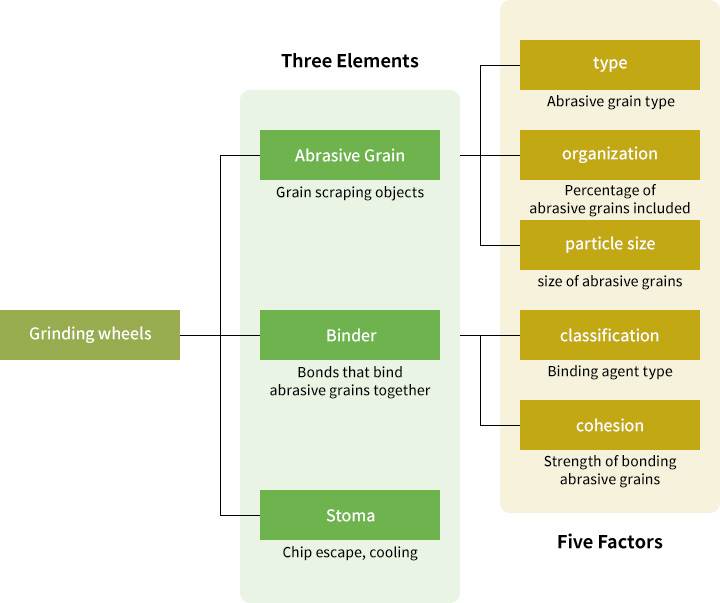
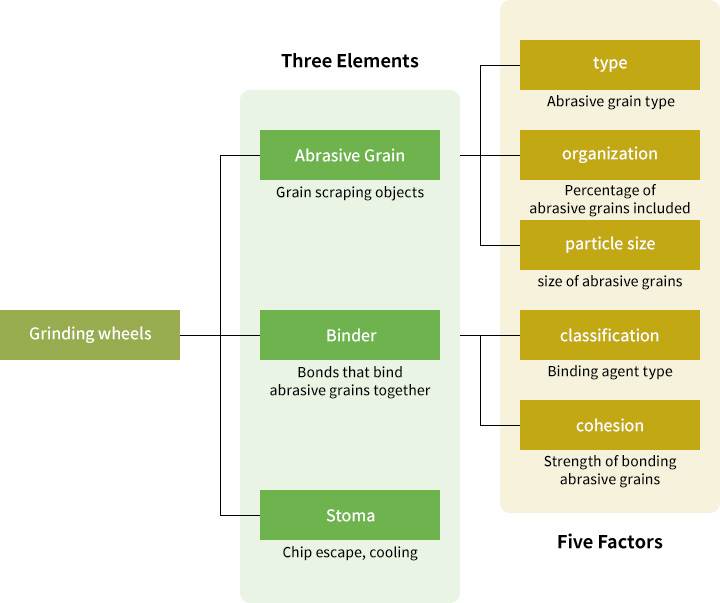
↑Tap image to enlarge
Grinding wheels are composed of three major components: abrasive grains, bonding agent, and pores.
These three are called the “Three Elements of Grinding Wheel”.
By varying the type and amount of these three elements, a wide variety of grinding wheels can be made.
The three elements are further classified into five categories: type of abrasive grain, grain structure, grain size, type of binder, and degree of bonding. These are known as the "Five Factors of Grinding Stones."
Abrasive grain
Sharpens the workpiece.
The abrasive grain, a crystalline particle of hard mineral, acts as the cutting edge in the grinding wheel.
Kinds
Classification | Name and type | Color | Feature |
---|---|---|---|
Alumina Grinding Material | A abrasive grain (alundum) Brown Alumina Grinding Material |
dark brown | Alumina material consisting mainly of bauxite is melted and reduced in an electric furnace, and the mass containing an appropriate amount of titanium oxide is pulverized. The crystal consists of 95-97% alumina and contains more impurities than WA abrasive grains. It has high toughness and is generally used for steel grinding. |
WA abrasive grain (white alundum) White Alumina Grinding Material |
white | Alumina refined by the buyer's method is melted in an electric furnace, and the solidified mass is ground and graded. It consists of white corundum crystals and is harder than A-abrasive grain, but its toughness is slightly inferior. However, it has good wall-opening property (crushability) and generates less heat, making it suitable for grinding work with a large contact area between the workpiece and the grinding wheel. | |
PA abrasive grain (pink alundum) Light red alumina abrasive |
pink | Alumina refined by the same buyer's process as WA to which appropriate amounts of chromium oxide, titanium oxide, etc. are added is melted in an electric furnace, and the solidified mass is ground and granulated. It is composed of corundum crystals in which the additives are individually dissolved. | |
HA abrasive grain Fractured Alumina Grinding Material |
Bauxite or alumina material prepared by the Beyer process is melted in an electric furnace, and the solidified mass is crushed and graded. Consists of a single crystal of corundum crystals. | ||
AE abrasive grain Artificial Emery Grinding Material |
grayish black | An alumina material consisting mainly of bauxite is melted and reduced in an electric furnace, and the solidified mass is ground and graded. Mainly composed of corundum and mullite crystals. |
|
AZ abrasive grain Alumina Zirconia Grinding Material |
gray | Alumina refined mainly by the Byers process is added to zirconia material, melted in an electric furnace, and the solidified mass is ground and graded. It is composed of corundum crystals and eutectic portions of alumina-zirconia. | |
Silicon carbide abrasives | C abrasive grain (carborundum) Black silicon carbide abrasive |
black silver grey |
This is a granulated product made by grinding and grading lumps of silicon oxide raw materials, consisting mainly of silica rock and silica sand, and coke, which are reacted in an electric resistance furnace. Harder than alumina-based abrasive grains, but less tough. |
GC abrasive grain (green carborundum) Green silicon carbide abrasive |
green | This is made by grinding and grading lumps of silicon oxide raw materials consisting mainly of silica rock and silica sand, and coke, which are reacted in an electric resistance furnace. It is harder than C-abrasive grains and has higher wall-opening ability. Not suitable for rough grinding and heavy duty grinding as the grinding wheel wears out quickly. | |
superabrasive grain | SD abrasive grain synthetic diamond |
It is superior to other grinding wheels in terms of heat resistance and abrasion resistance. Widely used in various fields from rough grinding to precision grinding. | |
CBN abrasive grain cubic boron nitride |
black dark reddish-brown |
Used for grinding difficult-to-machine materials that are difficult to grind with A-type abrasive grains. |
Organization
It is the content ratio of abrasive grains to the volume of the grinding wheel.
It is represented by a number from 0 to 14.
Organization | Abrasive grain ratio(%) | Tolerance(%) |
---|---|---|
0 | 62 | ±1.5 |
1 | 60 | |
2 | 58 | |
3 | 56 | |
4 | 54 | |
5 | 52 | |
6 | 50 | |
7 | 48 | |
8 | 46 | |
9 | 44 | |
10 | 42 | |
11 | 40 | |
12 | 38 | |
13 | 36 | |
14 | 34 |
When the grit ratio increases, the grit is packed tightly and looks dense. Conversely, when the grit ratio decreases, the grit looks crumbly.
For the same amount of the same binder, an increase in the abrasive grain ratio will result in weaker grain retention, more grain dropout, and softer action.
Conversely, if the grain ratio is reduced, the grain retention is stronger and the effective cutting edge is reduced, making it impossible to grind efficiently and resulting in a harder grinding action.
Particle size
It represents the size of abrasive grains and is generally expressed in the form of the number 00.
Types of abrasive grains by grain size (number) |
---|
4, 5, 6, 7, 8, 10, 12, 14, 16, 20, 24, 30, 36, 40, 46, 54, 60, 70, 80, 90, 100, 120, 150, 180, 220, 240, 280, 320, 360, 400, 500, 600, 700, 800, 1000, 1200, 1500, 2000, 2500, 3000, 4000, 6000, 8000 |
*4 is the coarsest and 8000 is the finest.
The finer the grain size (smaller abrasive grains), the better the finished surface, but the grinding capacity is reduced and more grinding heat is generated, which may cause grinding burning and chattering.
The granularity should be selected according to the purpose.
Binder
A material used to bond and hold abrasive grains together. Also called bond.
Kinds
vitrified | V | Made of feldspar and other inorganic clays as binder, it is water and chemical resistant and can be stored for long periods of time. Firing temperatures range from 1200 to 1300 degrees Celsius. |
resinoid | B | Also called the Bakelite method, this method uses coal acid and formalin-based synthetic resins as binding agents, and is highly elastic, tough, safe, and can be used at high speeds. |
rubber | R | Natural or artificial rubber is used as a binder. It is highly elastic, strong, and resistant to deep scratches, resulting in a beautifully finished surface. Weak against heat and oil. |
magnesia | Mg | A type of cement called magnesia oxalite is used as a binder, a property that is less adversely affected by grinding heat. For wet use, corrosion prevention measures are required. |
shellac | E | Natural resin (secretion of lac shellworm) is used as a binding agent and has the weakest binding strength. |
silicate | S | Sodium silicate (water glass) is used as a binder, and sodium silicate has a lubricating effect. Alkaline grinding fluid can be dangerous. |
metal | M | Uses metals such as silver, copper, and nickel as bonding agents and has the strongest bonding strength. It is mainly used as a binder for diamond and CBN. |
Cohesion
The degree of bonding is represented by letters A to Z, with A being the softest and Z being the hardest.
The hardness is measured using a Rockwell hardness tester, and the HRH values are classified from A to Z. The bonding degree standard and bonding degree range are then established and the bonding degree is classified.
In some cases, the RH of HRH is used to indicate the representative value measured by the Rockwell hardness tester.
Stomata
It acts as a pocket that temporarily stores chips and also collects cooling water and air to cool the heat generated.